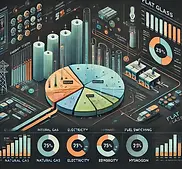
Energy Consumption Breakdown
Energy Breakdown of different configurations of quicklime decarbonisation
Energy Consumption and Emissions in Lime Kilns
Quicklime production necessitates high-temperature kilns to perform the calcination reaction, converting limestone into quicklime and COâ‚‚. This analysis compares eight kiln configurations based on energy demand and COâ‚‚ emissions:
​​​
-
NG – Conventional natural gas air-fired kiln
-
NGOxy – Natural gas oxy-fired kiln for concentrated flue gases
-
Plasma – Plasma-based electrified kiln
-
BioCH4 – Uses biomethane as a clean fuel
-
BioCH4Oxy – Biomethane oxy-fired kiln for concentrated flue gases
-
H2Oxy – Hydrogen oxy-fired kiln for concentrated flue gases
-
Biomass – Uses solid biomass (wood) as a clean fuel
-
BiomassOxy – Biomass oxy-fired kiln for concentrated flue gases
​
Energy Demand Components (GJ/t)​
-
Q-Process – Thermal energy for limestone calcination
-
EL-Process – Electrical demand for kiln operations
-
EL-ASU – Electricity for oxygen production in oxy-fuel systems​
-
Q-CCS – Heat required by chemical absorption-based COâ‚‚ capture
-
EL-CCS – Power required by absorption-based COâ‚‚ capture (Ch.Abs.) or cryogenic COâ‚‚ capture (CO2CPU)
-
EL-Electrolyzer – Electricity for green hydrogen production
​
Carbon Capture (CCUS) Impact
CCS increases energy demand due to COâ‚‚ separation and compression but reduces overall direct and indirect emissions per ton of lime. This analysis highlights key decarbonization strategies in industrial lime manufacturing.
​